
ACTIVATED CARBON FILTRATION SYSTEM
Activated carbon filtration system is a purification method used to remove unwanted organic matter, bad odor, taste and some chemicals (e.g. chlorine and VOCs - Volatile Organic Compounds) from water or air. The system provides purification of water or air using activated carbon material with high surface area.
Activated carbon is usually obtained from carbon-rich materials such as coal, wood or coconut shells, with high capacity and oxygen-free storage. The porous structure allows the physical and chemical retention of organic organisms and chemicals.
Areas of Use
-
Domestic: Drinking water treatment, removal of chlorine and bad odors from tap water.
-
Industrial: Purification of water for food, pharmaceutical, medicine and cosmetic products.
-
Wastewater Treatment: Removal of organic soot.
-
Air Filtration: Cleaning the air of bad odors and chemicals.
-
Aquarists: Cleaning the water in fish tanks.

Activated Carbon System General Components and TECHNICAL DETAILS 1. Activated Carbon Media Granular Activated Carbon (GAC): Generally used for bad taste, odor and chlorine removal. Block Activated Carbon (CTO): Provides both chemical and physical filtration with its compressed structure. Powdered Activated Carbon (PAC): Offers high surface area thanks to smaller personal computers, generally preferred for short-term use. Coconut Shell Carbon: Provides higher purity and its own density, available in drinking water treatment. Coal-Based Carbon: Used in industrial and heavy-duty facility removal. Function: Continues to adsorb formations such as chlorine, organic structures, bad taste and odor, organic organic structures (VOCs). 2. Filter Body Material: Made of polypropylene, stainless steel or durable plastic. Shape: Cylindrical or square structure, varies according to filtration change. Feature: Pressure resistant and leak-proof. Its function: To keep the activated carbon media safe and ensure that water circulates smoothly in the system. 3. Inlet and Outlet Connections Material: Stainless steel, brass or durable plastic. Dimensions: Manufactured in standard pipe diameters according to the parts of the system (e.g. 1/2", 3/4"). Function: Allows water or air to enter and exit the filter, optimized for smooth flow. 4. Pre-Filter (Optional) Material: Polypropylene or polyester. Filtration Accuracy: 5 microns or more. Function: Prevents the explosion of activated carbon by retaining large diseases, tortures and suspended solids. 5. Final Filter (Optional) Material: Synthetic fibers or ceramics. Function: The activated carbon catches the fine diseases that leave the filter, ensuring that the water is cleaner. 6. Pressure Gauges (Optional) Function: Monitors the operating data of the system. Advantage: Pressure loss indicates that the filter is clogged or the carbon medium has reached saturation. 7. Air Release Valve Function: It provides proper water distribution by discharging the air accumulated in the system and prevents performance loss. Area of Use: It is found in portable industrial systems. 8. Discharge Valve Function: It is used to clean the carbon period and discharge dirty water. Advantage: It provides the opportunity to clean without changing the carbon media during maintenance. 9. Backup System (Optional) Activated Carbon Backup Unit: A second unit to change the carbon media in the system. Advantage: It provides uninterrupted filtration. 10. Control Panel (Optional) Operation: To monitor the filtration process, control the pressures and distributions. Advantage: It provides a user-friendly distribution especially in industrial systems. 11. Sealing Elements Gasket and O-Rings: Provides sealing between the filter body and the inlet-outlet connections. Material: Rubber, silicone or Teflon. 12. Mounting and Support Devices Function: Provides cleaning of the filter system or fixing it to the ground. Material: Stainless steel or durable plastic. Advantage: Provides safe and stable operation of the system. 13. Water Flow Diverters Function: Optimizes the passage of water through the active carbon media and increases contact time. Advantage: Provides more effective filtration. 14. Automatic Washing System (Optional) Function: Extends the life of the active carbon media by regularly cleaning it. Advantage: Maintenance efficiency decreases especially in large industrial systems. The quality and correct design of this product directly affect the active carbon filtration system and durability. A system that is properly maintained and regularly maintained ensures effective purification of water or air.
Activated Carbon System Periodic Maintenance GENERAL MAINTENANCE PRINCIPLES Activated Carbon Filtration Systems Maintenance Activated carbon filtration results should be maintained regularly to ensure the continuity and longevity of the system. After a certain period of time, active carbon reaches saturation and does not retain parts. Therefore, it is important to perform regular checks and replace both the filter media and other regular checks. 1. Control and Replacement of Activated Carbon Media Change Period: How often to change activated carbon depends on the quality of the water used and the system parts: In domestic use: Every 6-12 months. In industrial use: Every 3-6 months or according to analysis. Signs: Deterioration in taste and odor of water. Decrease in water pressure. Filter loses target recording. 2. Filter System Cleaning Task: Cleaning of accumulated sediment, sludge or biological contamination inside the filter. Frequency: Every 3-6 months or during carbon change. Method: Clean the body with clean water and debris using a soft brush. 3. Checking and Changing Pre- and Post-Filters Pre-Filter: Prevents the explosion of activated carbon by holding large disturbances. Change Period: Every 1-3 months or in case of change. Post-Filter: Activated carbon change holds small irregularities. Change Period: Every 6-12 months. 4. Testing Water Quality Water quality testing can be done regularly for the evaluation of activated carbon. Parameters to be tested: Use chlorine level (if you use tap water). Taste and odor change. TDS (Total Dissolved Solids) value. 5. Air Evacuation Task: Evacuation of air accumulated in the system. Frequency: Air bubbles were observed during filtration. Method: Remove air from the system using the air evacuation valve. 6. Pressure and Flow Control Check the pressure gauge regularly: Low pressures: Indicates that the filters may be clogged. High pressures: Indicates that there may be a blockage in the system. Frequency: Weekly checks are recommended. 7. Chemical Cleaning (Optional) In Case of Biological Disease: If there is algae or bacteria formation in the system, chemical cleaning can be done. Use biocides or disinfectants suitable for active carbon for cleaning. Frequency: Once a year or distribution of biological pollution. 8. Drain and Drainage Control Task: Drain the system of accumulated dirty water using the drain valves. Frequency: Every 1-3 months or during carbon change. 9. Checking of Sealing Elements Seals and O-Rings: Ensure that the filter storage and connections are not leaking. Change Period: Should not be replaced immediately in case of wear. Frequency: Should be checked during maintenance. 10. Professional Service and Calibration In case of large separations or automatic systems, professional service is recommended once a year. System calibration should be done and the automation system (if any) should be checked. Maintenance Frequency Summary Table Maintenance Step Frequency Active carbon change Every 6-12 months Filter chamber cleaning Every 3-6 months Preliminary and final filter change Every 1-3 months Water quality test Monthly Pressure and Flow Weekly Air purge Requirement Chemical cleaning Annually or Administrator Seal and O-Ring check During each maintenance Nutrition Importance Performance: Protects the system. Economy: Long-term cost loss. Health: Provides cleaner and safer water. Longevity: Extends the service life of the system. Regular maintenance ensures that the active carbon filtration efficiency operates at maximum efficiency and provides long-term service.
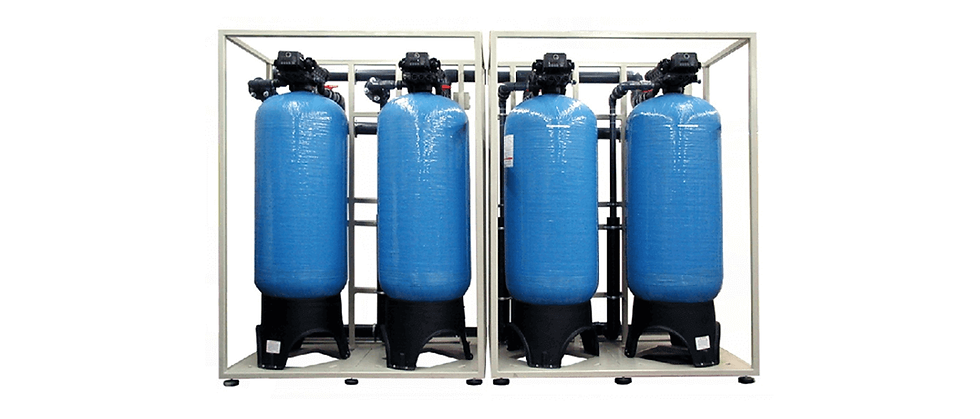
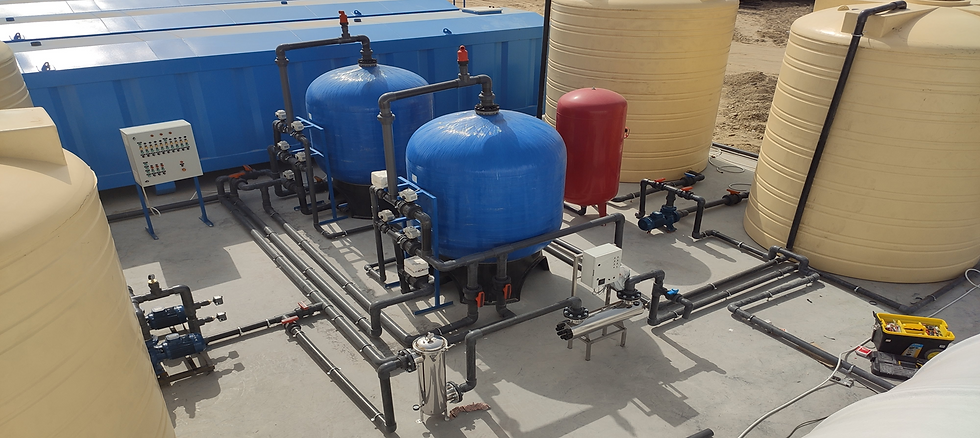

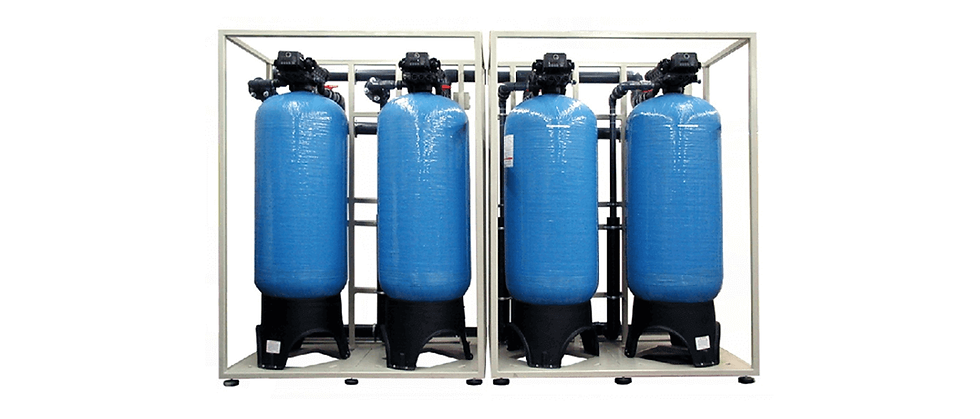
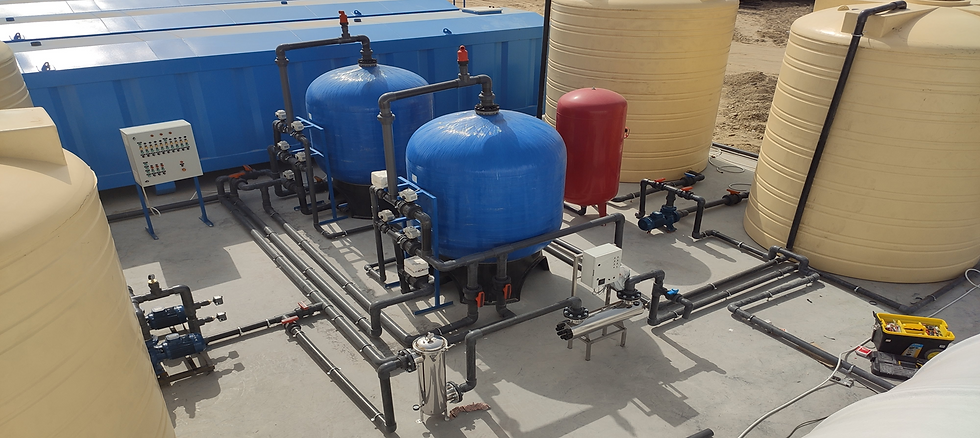


Engineer;
The engineering discipline aims to produce sustainable solutions based on the principle of "The Most Efficient Use of Resources with the Best Results".

Water Treatment Environment Dictionary
Our priority is to produce permanent solutions based on the principle of "Highest Efficiency with Lowest Cost", which is the main purpose of engineering.

Sıkça Sorulan Sorular
Our goal is to provide 100% customer satisfaction with sales and after-sales technical services to every region of Turkey.

Quality Certificates
Based on the importance of quality, customer satisfaction is always our top priority at every stage of our production.

Efficient and Effective Solutions
Mühendisliğin temel felsefesi, ''Az Maliyetle Yüksek Performans'' yaklaşımıyla, yenilikçi ve uzun vadeli çözümler geliştirmektir.